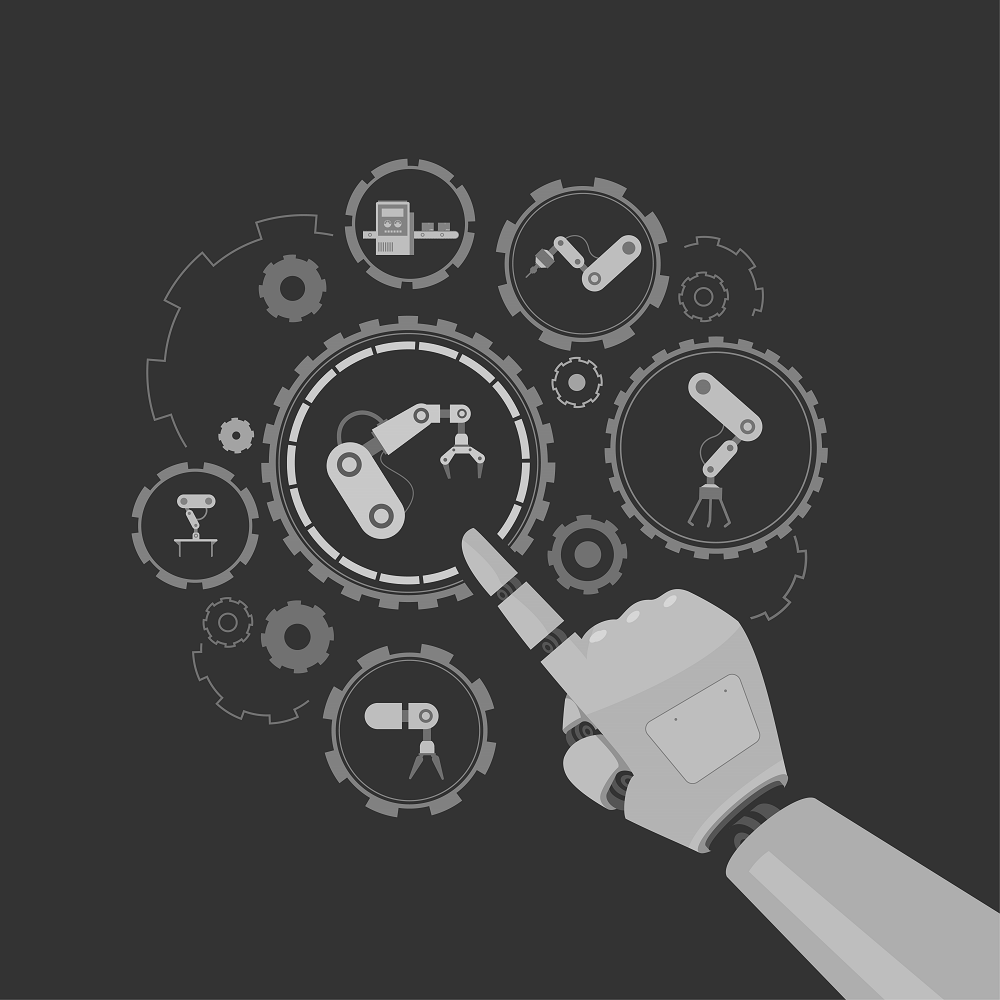
Composite Substitutes for Large Heat Exchangers: Cost Reduction through Innovative Materials
Heat exchangers are vital components used in a wide range of industries, including power generation, chemical processing, and HVAC systems. They transfer heat between two fluids to either cool or heat them, making them an essential part of many processes. Traditionally, heat exchangers are made using materials such as stainless steel, copper, and aluminum. However, these materials have limitations, including high cost, heavy weight, and limited resistance to corrosion and wear. The use of composite materials in heat exchangers presents a promising solution to these limitations, leading to significant cost savings and improved performance. In this article, we will explore the potential of composite materials as a substitute for traditional materials in large heat exchangers.
What are Heat Exchangers and Their Importance?
Heat exchangers are devices that transfer heat between two or more fluids, such as air, water, or steam, without the fluids coming into direct contact. They are used in a wide range of applications, including refrigeration, air conditioning, power generation, and chemical processing. Heat exchangers play a crucial role in these industries, as they enable efficient and effective heat transfer, which is essential for many processes.
What are the Current Materials Used in Heat Exchangers and Their Limitations?
Traditionally, heat exchangers are made using materials such as stainless steel, copper, and aluminum. While these materials are effective, they have some limitations. For example, stainless steel is expensive, copper is heavy and prone to corrosion, and aluminum has limited thermal conductivity. These limitations can lead to higher costs, reduced efficiency, and increased maintenance.
What are Composites and Their Advantages?
Composite materials are materials made from two or more constituent materials with different physical or chemical properties. The combination of these materials creates a new material with enhanced properties that can overcome the limitations of individual materials. Composites have several advantages over traditional materials, including high strength-to-weight ratio, corrosion resistance, and low thermal expansion.
What are the Properties Required for Composites to be Used in Heat Exchangers?
To be used in heat exchangers, composites must have specific properties. The most important properties include thermal conductivity, corrosion resistance, and mechanical strength. Composites used in heat exchangers must also have good dimensional stability, resistance to high temperatures, and compatibility with the fluids being transferred.
What are the Latest Developments in Composite Materials for Heat Exchangers?
Recent advancements in composite materials have made them viable alternatives to traditional materials in heat exchangers. For example, carbon fiber reinforced polymer (CFRP) composites have shown high thermal conductivity and strength, making them ideal candidates for heat exchanger applications. Other types of composites, such as polymer matrix composites and ceramic matrix composites, are also being developed and tested for heat exchanger applications.
What is the Potential Cost Savings of Using Composite Substitutes in Large Heat Exchangers?
The use of composite materials in heat exchangers can lead to significant cost savings for industries. Composite materials are lighter than traditional materials, which reduces the weight of the heat exchanger and associated support structures, leading to lower installation and transportation costs. Composite materials are also more corrosion-resistant than traditional materials, which reduces maintenance costs and downtime. A study by Composite Integration Ltd. found that a company in the oil and gas industry reduced their maintenance costs by 30% by using a composite heat exchanger in their offshore platform.
What Industries Can Benefit from this Innovation?
Industries that can benefit from the use of composite materials in heat exchangers include power generation, chemical processing, HVAC systems, and transportation. For example, in the power generation industry, the use of composite materials in heat exchangers can lead to improved efficiency, reduced downtime, and lower maintenance costs. This is because composite materials can withstand high temperatures and corrosive environments, which are common in power generation plants. In addition, the use of composite materials can also lead to a reduction in the size and weight of heat exchangers, which can lead to cost savings in transportation and installation.
In the chemical processing industry, composite materials can be used to resist corrosion and abrasion caused by chemicals, which can extend the lifespan of heat exchangers and reduce maintenance costs. In HVAC systems, composite materials can improve energy efficiency and reduce the size and weight of the heat exchangers, making them more cost-effective and easier to install. In transportation, the use of composite materials can lead to weight reduction, resulting in fuel savings and reduced emissions.
The Potential Cost Savings of Composite Substitutes in Large Heat Exchangers
One of the main advantages of using composite materials as substitutes for traditional materials in heat exchangers is the potential cost savings. The use of composites can reduce the cost of manufacturing and installation, as well as reduce maintenance costs, leading to significant cost savings over the lifetime of the heat exchanger.
According to a case study by Composite Integration Ltd., a company in the oil and gas industry was able to reduce their maintenance costs by 30% by using a composite heat exchanger in their offshore platform. The company also reported that the composite heat exchanger was lighter and easier to install than traditional heat exchangers, which resulted in additional cost savings.
In addition, the use of composite materials can also reduce the overall cost of the heat exchanger by improving efficiency and reducing the size and weight of the heat exchanger. This can lead to cost savings in transportation and installation, as well as energy savings over the lifetime of the heat exchanger.
Latest Developments in Composite Materials for Heat Exchangers
In recent years, there has been significant research and development in the use of composite materials for heat exchangers. Researchers are exploring new composite materials and manufacturing techniques to improve the properties of the composites and make them more suitable for heat exchanger applications.
Carbon fiber reinforced polymer (CFRP) composites have shown high thermal conductivity and strength, making them ideal candidates for heat exchanger applications, according to a study published in the Journal of Materials Science. Other types of composites being studied for heat exchanger applications include ceramic matrix composites (CMCs), metal matrix composites (MMCs), and polymer matrix composites (PMCs).
Manufacturing techniques are also being developed to improve the properties of the composites and make them more cost-effective. One such technique is called pultrusion, which involves the continuous pulling of fibers through a resin bath and then through a heated die to form the composite material. This technique can produce composites with high strength and thermal conductivity, making them ideal for heat exchanger applications.
Conclusion
Composite materials offer significant advantages over traditional materials for heat exchanger applications, including improved efficiency, reduced weight, and lower maintenance costs. Industries such as power generation, chemical processing, HVAC systems, and transportation can all benefit from the use of composite materials in heat exchangers.
Research and development in the use of composite materials for heat exchangers are ongoing, with new composite materials and manufacturing techniques being developed to improve the properties of the composites and make them more cost-effective. The potential cost savings of using composite materials in large heat exchangers can be significant, making them an attractive option for industries looking to improve their efficiency and reduce their costs.
Mechanical Engineering